From Order To Delivery: Optimising Logistics With Automated Fulfillment Systems
Explore enhanced logistics efficiency through automated fulfillment systems, optimising every step of the supply chain.
Customer expectations for fast, affordable delivery are intensifying pressure on retailers and logistics providers. Manual, labour-intensive fulfilment struggles to achieve the speed, accuracy and cost-effectiveness demanded today. Automated fulfilment systems offer a solution, integrating advanced robotics, AI and sophisticated software to optimise workflows. This article will examine key technologies powering automated fulfilment and analyse how they can enhance logistics capabilities across the order lifecycle.
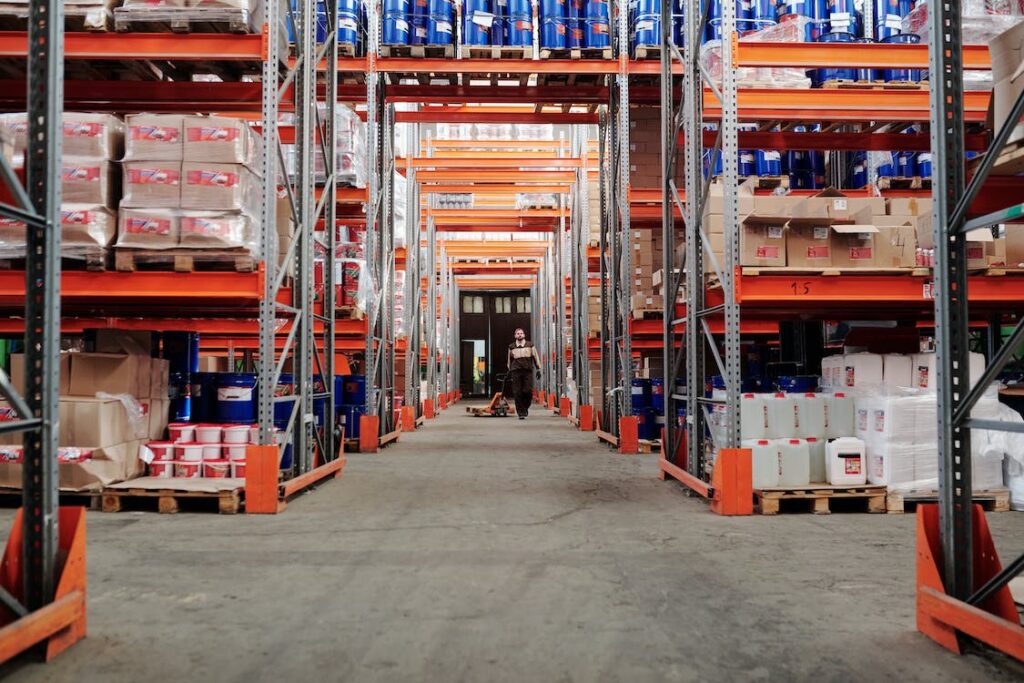
Automating Order Taking and Processing
The fulfilment process starts by capturing customer orders across channels. Previously manual tasks like taking phone orders or keying in e-commerce orders are now automated through AI chatbots and order management software. Chatbots handle routine customer inquiries with natural language processing. Order data seamlessly flows into warehouses and ERP systems, eliminating rekeying. Document processing software extracts order details from emails and faxes. Machine learning techniques validate addresses, cross-check product/inventory availability and implement fraud checks. Automating order-taking accelerates intake while reducing errors.
Optimising Warehouse Design and Layout
Automated systems allow warehouses to be designed for optimal material flows and storage density without the constraints of manual labour. Software simulations based on SKU dimensions, order profiles and equipment capabilities create customised layouts tailored to specific inventory. Narrower aisles, taller racks and tightly spaced pick locations become possible. Automated storage and retrieval systems can handle volumes too large or heavy for human pickers. Straight-line, high-speed conveyors replace winding routes. Adaptable, modular layouts reconfigure to changing needs. Simulation modelling ensures warehouse designs deliver the lowest processing times and costs.
Automated Inventory Planning and Replenishment
Automated systems can also optimise inventory planning and replenishment. Supply chain analytics generates stocking recommendations for each item based on demand forecasts, lead times, seasonality and other variables. Machine learning algorithms dynamically adjust stock levels and reorder points. Real-time inventory visibility through barcodes, RFID and IoT sensors enables precise monitoring across the warehouse. When levels drop below-defined thresholds, automated purchase orders are triggered to suppliers to replenish stock. Removing human planners’ biases and gaps results in optimal inventory availability and turnover.
Accurate Picking and Assembly
Picking is one of the most labour-intensive aspects of fulfilment. Mobile robots now automate pick paths to efficiently retrieve items from shelves based on order requirements. Their advanced vision systems confirm picks with 99%+ accuracy. Automated cranes and carousels provide access to items in deep storage locations. Smart conveyors merge individual orders and route them for packing. Automated storage and retrieval systems deliver entire pallets or totes to workers. Packaging robots custom-build boxes to precisely fit items, reducing material waste. Automating picking slashes processing times and errors.
Streamlined Packing and Shipping
After picking, automated systems complete packing and shipping preparation tasks. Stations apply labels, verify weights and dimensions, inject air pillows and seal boxes with tamper-proof tape. Some systems even construct custom cardboard boxes on demand to minimise shipping volume and cost. Conveyors sort packed parcels by destination zip codes and transport modes to facilitate loading onto outbound trucks. Computer vision systems recognise items to prevent shipping errors. Compliance labelling, customs documentation and manifests are auto-generated. This automation eliminates tedious manual processes to enable faster, more consistent shipping.
Real-Time Monitoring and Texting
Automated fulfilment technology also enables advanced shipment monitoring and customer communication capabilities. IoT sensors track parcel locations and conditions throughout delivery in real-time. Text and email alerts notify customers at each milestone from warehouse departure to proof of delivery. Machine learning models forecast expected delivery dates and flag potential disruptions proactively. Chatbots handle common customer inquiries about order status using natural language capabilities. Providing this real-time visibility and intelligent communication creates superior delivery experiences.
Continuous Optimisation via Analytics
The data from automated systems creates a feedback loop for ongoing optimisation. Machine learning algorithms identify new ways to streamline workflows using historical data. Predictive analytics forecasts periods of peak demand to preemptively adjust capacity. Monitoring utilisation and traffic patterns inform warehouse layout redesigns. Algorithms dynamically re-slot inventory to minimise fulfilment time. Automated reporting highlights performance across all logistics metrics to identify improvement opportunities. Built-in analytics enable automated fulfilment to continuously improve over time.
Enabling Omnichannel Logistics
Automated fulfilment capabilities readily support omnichannel distribution strategies. Orders from the website, smartphone apps, retail stores, contact centres and marketplaces are aggregated into a single optimised workflow. Inventory is effectively shared and visibility is centralised across channels. Automated transfers enable quick fulfilment from any node – warehouses, stores or pickup points. Customers gain flexibility in delivery speed, location and cost. Fulfillment resources are leveraged across channels for efficiency. Automation facilitates the complex orchestration required for true omnichannel logistics.
Empowering a Hybrid Workforce
It is important to note automated systems empower human workers rather than fully replacing them. Automation handles dangerous, dull, dirty and repetitive tasks, freeing humans to focus on value-added activities like complex problem-solving, relationship-building and continuous improvement. Workers monitor automated equipment, handle exceptions and quality-check shipments. Combining the strengths of humans and machines creates a robust, scalable fulfilment engine. Upskilling staff and thoughtful change management ensures a smooth transition to hybrid work.
Conclusion on Optimising Logistics With Automated Fulfillment Systems
Fulfilment automation is a competitive imperative for retailers to meet escalating consumer delivery expectations. Intelligently integrating robotics, software and data analytics optimises logistics workflows end-to-end. Superior speed, accuracy, visibility and flexibility are achieved. While automating fulfilment requires upfront investment, the long-term benefits are well worth the cost. Companies that embrace automation send a strong message that customer satisfaction is paramount. Adopting emerging technologies establishes a platform for staying at the forefront as logistics evolve.
Contact Us
We are here when you need us. Get in contact to see what we can do for you
Contact Us