Strategic Storage: A Comprehensive Guide To Warehouse Management In UK Freight Industry
Manual for strategic warehouse management in the UK freight industry
Warehousing is an essential component of the UK’s freight and logistics sector. Storage capabilities allow inventory, equipment and packaged goods to be handled in transit between producers, distributors and end consumers. Sophisticated warehouse management underpins efficient supply chains and frictionless commerce. This guide explores key aspects of strategic storage and best practice warehouse operations for UK freight companies.
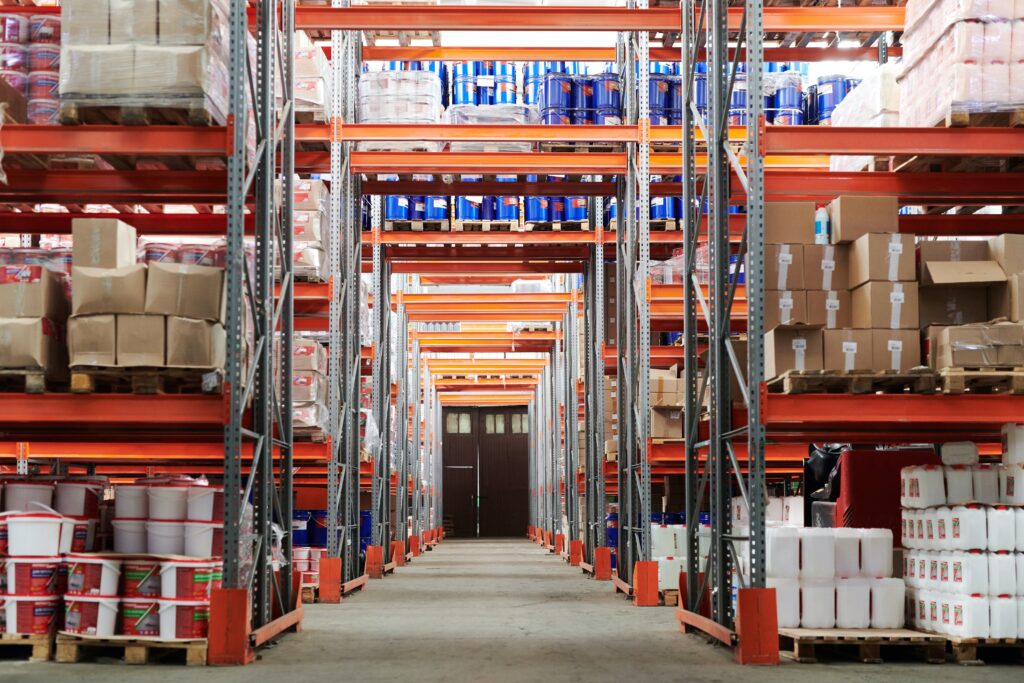
Warehouse Functions
Warehouses serve a range of valuable purposes including:
Consolidation – Combining smaller deliveries/shipments into fuller loads
Break Bulk – Separating larger consignments into smaller customer-specific orders
Cross Docking – Directly transferring goods between inbound and outbound vehicles
Transhipment – Changing between transport modes
Inventory Storage – Holding reserve stocks and staging order fulfilment sequences
Value Added Services – Packing, labelling, light assembly to ready orders for dispatch
Returns Processing – Inspecting, repackaging and refurbishing unwanted items
Strategic warehousing enables freight companies to optimise logistics flows through staging, aggregation and value-adding. Storage capabilities are tailored to supply chain needs.
Warehouse Locations
When establishing warehouses, logistics-oriented location planning is key. Sites should align to customer base, transport links, labour supply and freight intersections.
In the UK, major clusters of warehousing space lie near seaports, motorways, rail terminals and urban centres. ‘Golden Triangle’ regions like the Midlands provide prime distribution locations.
Larger warehouses of 10,000+ sqm suit outlying distribution park settings better than expensive urban zones. Smaller urban warehousing maintains city inventory and fulfilment functions.
Proximity to customers, multimodal infrastructure and freight corridors enables efficient in/outbound logistics. Planning law and community sentiments must also be considered in site selection.
Warehouse Design
Warehouse design requires balancing many operational parameters including:
Desired storage capacity
- Material flows and linkages between zones
- Inventory control and order fulfilment processes
- Access points and traffic flows
- Staffing, equipment and IT system requirements
Safety regulations and risk assessments
Customising layouts to match function is key, be it high throughput ‘pick face’ racks or specialised cold storage. Signposting, security, services and IT infrastructure enable smooth operations.
Adaptable building features facilitate reconfiguration as needs evolve. Lean principles help optimise floorspace use, workflows and waste reduction. Optimised design enhances warehouse productivity, quality and cost efficiency.
Storage Systems
Warehouses utilise a range of storage equipment tailored to the type of inventory held. Common systems include:
Pallet Racking – Adjustable bays for pallets accessed by forklifts
Shelving – Multi-level shelves suitable for smaller items and ‘pick and pack’
Upper Level Floors – Partial upper storeys effectively double floor space
Stacker Systems – Double-deep storage with mobile carriages accessing rear pallets
High Bay Racking – Narrow aisles with reaching forklifts facilitate dense storage
Automated Storage/Retrieval Systems – Cranes and shuttles automatically handle stock units
Storage systems aim to maximise capacity, accessibility and inventory control. Ergonomics and fire safety are also design factors. Automation is increasingly deployed for faster, denser storage in high-throughput warehouses.
Inventory Management
Knowing exactly what stock is held and where items are located in a warehouse is crucial for order accuracy. inventory management has advanced through technologies like:
Barcode scanners – Track stock locations and support order picking
Radiofrequency identification (RFID) – Provide individual item visibility via emitted signals
Voice picking – Headsets direct pickers with vocal commands
Pick-to-light – Illuminated displays guide picking sequences
Warehouse management systems – Centralised software organises inventory and workflows
These technologies enable real-time visibility of warehouse contents and movements. Cycle counts also help verify indexed stocks match actuality. Lean stock control and just-in-time review prevent oversupply.
Order Fulfilment
Processing customer orders requires efficient picking, packing, shipping preparation and load building. Batching orders for route-optimised delivery runs improves productivity.
Mobilising pickfaces via trolleys, RF scanning and voice direction enables rapid fulfilment. Automated sorting and conveyors prep completed orders for dispatch. Final mile carriers integrate via warehouse management system APIs.
Same-day and next-day deliveries are facilitated by minimising processing times. Strategic late customs clearance also helps staged export movements. Investment in fulfilment technology and workflows is key to high performance.
Materials Handling
Moving stock, pallets and parcels through warehouses requires reliable materials handling equipment like
Pallet trucks – Move pallets via hydraulic pumping or motors
Stackers – Forklifts for vertical storage access
Reach trucks – Narrow aisle forklifts that ‘reach’ within racks
Order pickers – Access multi-level racking from elevating cabins
Conveyors – Automated parcel and package handling
Automated Guided Vehicles – Self-driving trolleys follow floor magnets
Ergonomics, training and maintenance keep equipment productive. Hybrid power or alternative fuels reduce emissions. Automating transport between zones boosts throughput velocity. Materials handling innovations continue advancing warehouse capabilities.
Safety and Compliance
Warehouse operations are governed by extensive health and safety regulations. Key elements include:
Traffic management – Safe movement of vehicles and personnel
Shelving inspections – Ensuring integrity and stability
Equipment certification – Testing and inspection regimes for lifted assets
Training – Operating procedures and hazard awareness
PPE Requirements – High visibility clothing, gloves, footwear etc
Warning Signage – Clear identification of risks and instructions
Robust policies, supervision and technology like proximity sensors facilitate safety. Prevention of major incidents through risk management is paramount. Strict protocols apply for hazardous materials handling. Warehouse compliance is a legal necessity and a moral imperative.
Sustainability
Environmental sustainability is a growing logistics focus including warehouse operations through:
Energy efficiency – Lighting, heating and plant upgrades
Renewable power – Solar panels, battery storage, EV charging
Building standards – Optimised insulation, glazing and materials
Waste management – Water conservation, recycling streams
Supply chain integration – Shared storage, backhauling synergies
Smart routing – Minimised distances, strategic stock positioning
Sustainable warehouse design, technology selection and operating practices drive improved footprint. This is reinforced through company ESG policies and codes of conduct applied to service providers. Greener warehousing appeals to ethically minded clients.
Automation Technologies
Automating warehouse processes provides major productivity and accuracy gains. Technologies applied include:
Automated storage and retrieval systems – use automated cranes and shuttles to handle stock units without human intervention. This enables rapid, accurate inventory transactions monitored through a warehouse management system.
Goods-to-person picking – Conveyors and robotics deliver specifically required items to picking stations rather than pickers locating stock. Enables optimised workflows.
Automated guided vehicles – Self-driving mobile robots assist floor movement and handling tasks improving speed, safety and reliability.
Autonomous mobile robots – Handle repetitive tasks like transporting shelves to pickers or moving pallets between zones.
Robotic picking – Robotic arms populate orders using vision systems and AI to handle diverse objects. Greatly improves speed and accuracy.
Warehouse automation enables high-density storage, optimised workflows and 24/7 operation. It increases flexibility to handle business growth and seasonal peaks.
Final Thoughts On Warehouse Management In UK Freight Industry
Efficient warehouse operations are fundamental to effective freight distribution and supply chains. Optimising design, technologies, inventory control and order processing creates a strategic advantage.
Tighter integration of warehousing with broader transport networks and supply chain partners facilitates frictionless logistics. Smarter, sustainable warehouses will be at the core of industry evolution.
Contact Us
We are here when you need us. Get in contact to see what we can do for you
Contact Us