How To Achieve End-To-End Visibility In Freight Management
Navigate freight management challenges with end-to-end visibility. Unlock insights to enhance efficiency and streamline logistics.
End-to-end visibility provides logistics managers and cargo owners with real-time tracking and insight across the entire supply chain journey. This enables informed decisions through true situational awareness. With complex global supply chains and pressure to deliver products faster than ever, having visibility into the location and status of shipments is no longer just a nice-to-have—it’s a must-have. Building comprehensive visibility is invaluable but requires careful integration of processes, data sharing and technology. This guide explores key elements for successful implementation.
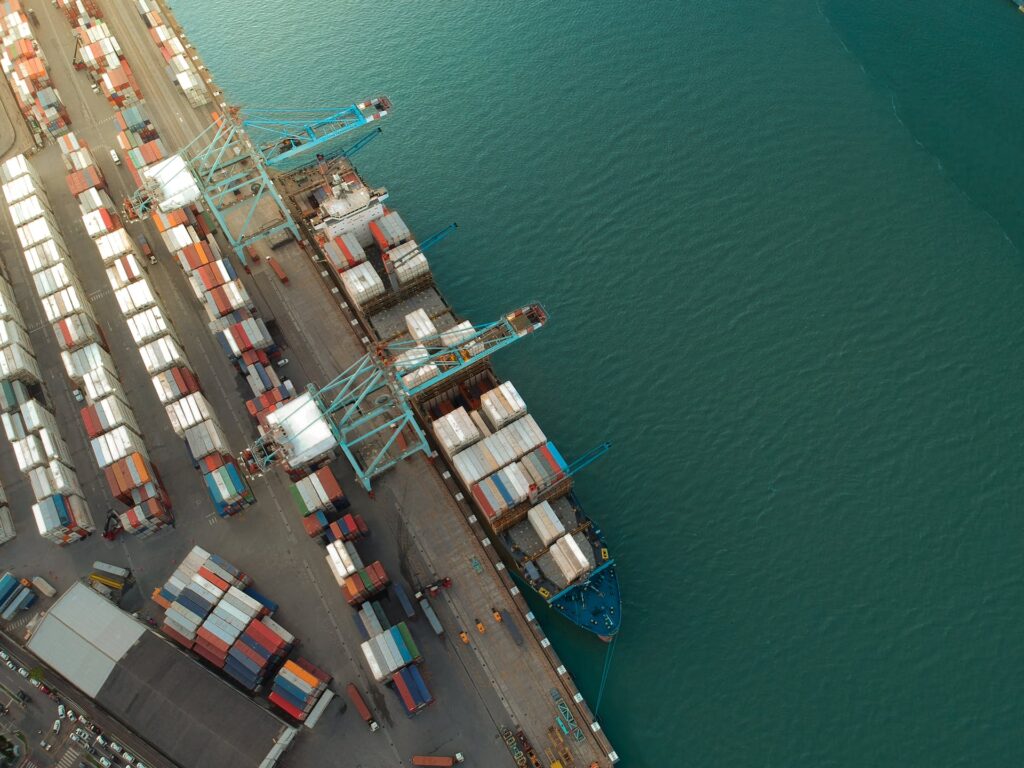
Implement a Unified Transportation Management System
The foundation for enabling end-to-end visibility is implementing a unified Transportation Management System (TMS) that connects the entire supply chain on a single platform. Rather than having disjointed systems for different transportation modes or regions, a single TMS provides one source of truth across the organisation. Key features to look for include:
Real-Time Tracking Capabilities
A TMS should facilitate real-time tracking across all freight types and regions. This includes connectivity to telematics devices, IoT sensors, and network cameras to capture real-time visibility data. The system should consolidate this data and make it accessible on a centralised dashboard with map views, milestone updates, and analytics. This enables all stakeholders to monitor shipment locations and status from pickup to final delivery.
Analytics and Reporting
Look for robust analytics in a TMS that synthesises visibility data into actionable insights. Users should be able to generate standard or custom reports that identify bottlenecks, optimise routes, compare carriers, and more to continually improve freight efficiency. These insights enable smarter supply chain and logistics decision-making.
Alerts and Workflow
Configurable alerts keep appropriate staff automatically notified of delays, exceptions, or arrival milestones. This facilitates rapid response to issues that threaten on-time delivery. Likewise, supporting workflow equips staff to handle responses efficiently through connected systems rather than manual processes.
Implement IoT Devices and Sensors
While a TMS serves as the central nervous system, IoT devices and sensors are the eyes and ears feeding real-time data into that system. Common technologies include:
GPS Trackers
Installing GPS trackers on trucks, containers, railcars and other transport conveyances enables precise location tracking throughout the shipment journey. Staff can see exact locations, verify times of key milestones like pickup and delivery, and receive alerts based on configurable geofences.
Sensors
Sensors can detect a wide range of environmental conditions, shipment status, and risk factors in transit. Examples include sensors that track temperature, humidity, shock, tilt, intrusion detection, and other metrics. Out-of-bounds readings trigger alerts so issues can be addressed before causing damage or delays.
Cameras
Fitting transport conveyances with network cameras adds additional visual verification. Users can remotely view inside containers or truck trailers to verify loading status, lock seal numbers, temperature probe accuracy and other data points. This facilitates remote inspections and problem resolution without costly, time-intensive physical visits.
Connect Partners via API Integration
Gaining end-to-end supply chain visibility requires connecting data from partners up and downstream along with internal systems. A TMS should facilitate this via open API connectors that allow quick integration to 3PLs, carriers, warehouses, seaports, vendors and more. This brings external data directly into the centralised platform rather than relying on manual data transfers.
Particularly valuable are connections to last-mile carriers. Tracking final delivery trips historically presented a blind spot for many shippers—an API integration fills this crucial gap in visibility. This integration also drives efficiencies for the carrier by equipping their drivers with routing, electronic proof of delivery, and other capabilities through the TMS mobile app.
Unify Cross-Departmental Data
Ideally, a TMS also centralises supply chain data from across internal enterprise systems into a single interface for different departments. Consolidating transportation, inventory and order data delivers true end-to-end visibility in one intuitive interface while encouraging cross-departmental collaboration. Staff spend less time tracking down shipment status updates and can instead focus on more value-added work.
Establish Standard Operating Procedures (SOPs)
With the technology foundation established via TMS implementation, companies must develop SOPs to maximise those enablement capabilities. Examples of key SOPs include:
Asset Tracking Processes
Define consistent processes for associating asset-tracking devices with specific vehicles, drivers, containers, trailers and conveyances. This includes naming conventions to tie the unique device ID to the asset and corresponding identifier in the TMS. It also requires procedures for securely mounting devices and confirming accurate data transmissions before transit.
TMS Data Entry Rules
Standardise how staff enter supplemental shipment data not fed directly from IoT sensors or partners. This includes identifying required order, shipment and item-level reference fields needed to link external data sources. It should also guide best practices for entering case counts, packaging types, images and other valuable data elements.
Alert Procedures
Determine appropriate alert routing and escalation procedures tailored to different scenarios like temperature excursion, late delivery, traffic delays and more. Clearly define individual or group responsibilities and sequences of accountability for responding to critical event alerts.
Carrier Scorecarding Policies
Leverage robust TMS data to objectively scorecard and compare network carriers on key performance indicators like on-time rate, claims ratio, responsiveness and data connectedness among other criteria. Use scorecards to guide both performance incentives and corrective action discussions aimed at continuous improvement.
Develop Dashboards for Each Role
With so much data now available, define visibility dashboards tailored to each staff role across departments like logistics, customer service, procurement, planning and warehouse/transport managers. Clear data accessibility for specific responsibilities empowers staff and reduces dependency bottlenecks. Provide self-service reporting tools supplemented by options to request custom analytics support as needed.
Final Thoughts on Freight Management
Implementing these steps will drive meaningful progress toward achieving end-to-end visibility across the supply chain. The ability to proactively track shipments in real-time, receive critical alerts, and generate insightful analytics unlocks game-changing potential. Companies can better mitigate disruptions, delight customers with delivery transparency, optimise routes, and audit partners, resolve issues faster and guide strategic decision-making. With incrementally expanding capabilities, leaders position themselves to continually extract more value over time from their freight and supply chain data assets.
Contact Us
We are here when you need us. Get in contact to see what we can do for you
Contact Us