Creative Solutions To Reduce Supply Chain Costs
Find creative ways to reduce operating freight and supply chain costs.
Supply chains present one of the largest cost centres threatening business profit margins today. Rising transportation costs, labour shortages, inflated component pricing, and disruptive events put immense pressure on supply chain expenses. Companies wanting to stay competitive must find creative solutions to reduce supply chain costs.
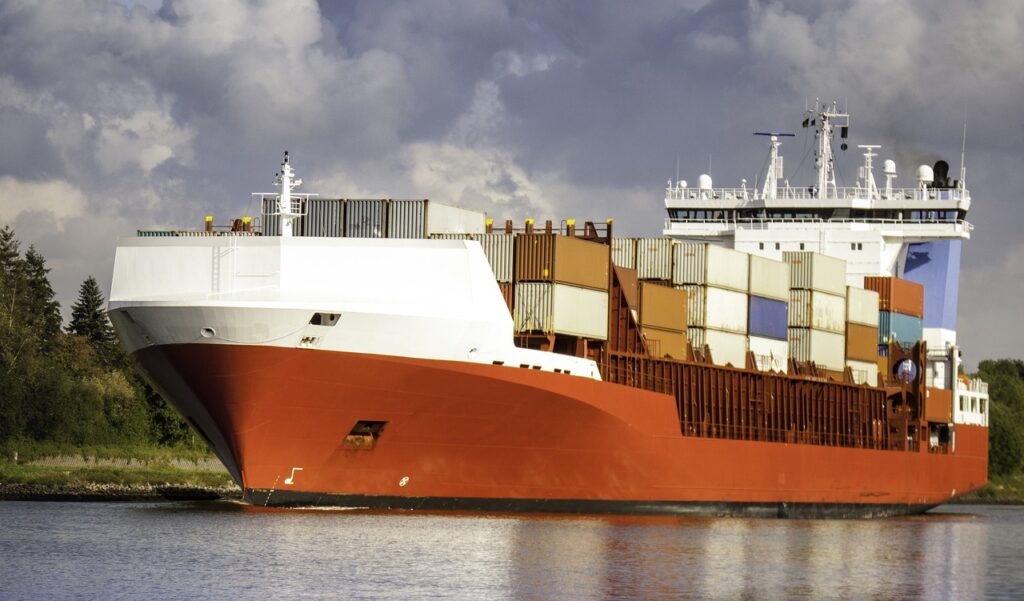
This comprehensive guide details innovative tactics to trim annual supply chain spend without impacting quality or outcomes. Learn smart and creative solutions to reduce supply chain costs around optimising processes, technology integration, scaling production, strategic partnerships, and more.
Analyse Processes End-to-End To Find Savings
Taking a holistic view across the entire supply chain uncovers savings opportunities missed when looking only at individual functions. Map out current state processes from sourcing and procurement to final mile delivery.
Scrutinise pain points around outdated workflows, unused features in supply chain tech stacks, or redundancies indicating waste. Brainstorm fresh approaches or use change management methods to reimagine smarter ways to structure operations. Even longstanding processes eventually need revamps to cut costs.
Leverage Predictive Analytics Tools
Sophisticated analytics platforms integrating historic datasets, machine learning algorithms, and market signals better predict demand swings, inventory needs, and freight expenditures. Investing in reliable predictive analytics substantially curbs overordering, stockouts, obsolescence, and markdowns.
Data-savvy supply chain leaders access advanced decision support to optimise everything from staffing to transportation mode usage. Look beyond basic analytics and reporting tools your company currently uses.
Renegotiate With Core Suppliers
Over time, core suppliers increase pricing or decrease service levels slowly by counting on customer complacency. Revisiting longtime supplier contracts often yields discounts, especially when volumes ramp up significantly.
Before contract renewals, approach incumbent suppliers highlighting new shipment frequencies, size, or sustainability preferences. Then request revised pricing reflecting your shift in buying power and importance to them. With trust earned, negotiations often progress quickly.
Pursue Strategic Supplier Partnerships
Transforming transactional vendor relationships into strategic partnerships promotes mutual investment in supply chain innovations to reduce costs longer-term. Collaborating on forecasting, lean initiatives, custom orders, or capacity planning often yields efficiencies exceeding short-term vendor discounts.
Committed partners gladly exchange actionable data, adjust processes, and invest in tech integration that unlocks savings for both parties. If suppliers shun transparency or innovation, consider shifting business elsewhere.
Scale Production Capabilities
Manufacturers scaling production through facility expansions, increased shifts, or updated equipment gain better economies of scale. Producing higher volumes at an optimised cost per unit saves exponentially.
Building out manufacturing slowly overutilises costly fixed assets like facilities, machinery, and salaried staff. Smart scaling analysis indicates the ideal facility footprint and production volumes to minimise per-unit costs. These shifts require upfront capital but deliver major savings.
Offload Shipping To Trusted 3PLs
Outsourcing shipping operations to qualified third-party logistics (3PL) providers reduces transportation and warehouse costs for many enterprises. Experienced 3PLs efficiently consolidate volumes across clients to secure reduced parcel, LTL, FTL, and ocean freight rates.
More importantly, the best 3PLs operate extremely sophisticated transportation management systems you rarely can replicate internally. Lean 3PLs also flex staff and assets to precisely fit volumes, thereby cutting labour and equipment carrying costs.
Integrate Automation Technologies
Automating repetitive, error-prone supply chain tasks using AI, intelligent workflows, robotics, and modern ERP/WMS systems are some more creative solutions to reduce supply chain costs while substantially decreasing payroll costs.
Evaluate potential automation across order processing, inventory moves/tracking, transportation booking, freight auditing, reporting and more. Prioritise high-impact changes delivering the fastest ROI through staff time and productivity gains.
Modify Production Batch Sizes
Analysing ideal production batch sizes balances the competing costs of setup versus holding excess stock. Both smaller batches and larger batches can waste money and resources. So fine-tuning manufacturing plans to minimise total costs offers big wins.
Carefully determine optimum production cycle times and inventory buffer volumes – not too big or too small. Simulation modelling delivers data-based recommendations before retooling physical processes.
Centralise Key Facilities Strategically
Examining facility locations with network optimisation tools pinpoints opportunities to centralise operations while still meeting customer lead times. Consolidating production, packaging, or distribution from smaller dispersed buildings into larger centralised campuses reduces fixed overhead costs significantly.
But beware of analysis paralysis. Gain 80 per cent + of potential savings from obvious centralisation moves before losing momentum. Follow the data, make decisions, and track impacts.
Outsource Non-Core Supply Chain Functions
Focusing internal staff on executing core supply chain competencies well enables offloading peripheral functions to specialised outsourcing firms. Contracting vehicle maintenance, security services, canteen/cafeterias, landscaping, janitorial work, and even accounts payable can cost less than managing in-house.
Leverage outsourcer scale economies and process expertise to save. But retain control over functions directly impacting quality or customer experience since poor outsourcing breeds failure.
Sell Excess Equipment And Materials
Supply chains fluctuate over time, leaving overcapacity in various assets, supplies, and materials. It becomes important to opt for creative solutions to reduce supply chain costs. Rather than scrapping extra equipment, sell to brokers or wholesalers recouping some residual value. Quality used assets get new life while clearing your balance sheet.
Examine inventory for reusable or recyclable materials acceptable for selling to scrap dealers or materials traders. Removing waste responsibly generates small revenue while optimising working capital needs.
Right-Size Transportation Resources
Oversised transportation resources like extra trucks, bloated container inventories, underutilised trailers, and costly expediting services bloat supply chain budgets. Examine carrier contracts, shipment histories, and lane requirements to right-size fleets across modes.
Consolidate volumes for better utilisation using experienced freight brokers. Sell or lease excess rolling stock is not needed. Replace expedited shipping with improved planning and forecasting. Resources balances enable savings.
Install Energy Efficient Facility Upgrades
With buildings and plants accounting for over 40 pe cent of supply chain carbon emissions, prioritising sustainability also trims energy costs. Simple upgrades to LED lighting, improved insulation, high-efficiency HVAC systems, solar panels, heat recycling, and electric forklifts deliver ongoing utility savings.
Government and utility incentives can offset upfront installation costs for major retrofit projects. Lower emission facilities also strengthen compliance, disaster resilience, employee retention and risk management.
Key Takeaways – Creative Solutions To Reduce Supply Chain Costs
With proper analysis and creative solutions to reduce supply chain costs, companies can reimagine processes and partnerships to substantially lower supply chain costs in a transformative way. Top tactics offer both immediate and long-term savings across core operating expenses:
- Process optimisation identifies redundant efforts to streamline
- Predictive analytics and simulation models guide data-backed decisions
- Strategic supplier and 3PL partnerships drive innovation
- Scaled production, automation, and facility centralisation improve productivity
- Right-sized logistics resources and selling excess assets curb waste
Finding creative solutions to reduce supply chain costs requires upfront investments offset by major savings over 2-3 years. Smaller tweaks accumulate bigger bottom-line impacts too. With margins tight and scrutiny high, supply chain leaders must pursue every opportunity to cut costs.
Contact Us
We are here when you need us. Get in contact to see what we can do for you
Contact Us